Prozesse in der Produktion: Ausblick auf eine rosige Zukunft
Anbieter zum Thema
Industrielle Revolutionen haben unsere Arbeitswelt stets grundlegend verändert. Dabei ist das Verhältnis des Menschen zur Veränderung äquivalent. Für die Produktion bietet sich der Ausblick auf eine rosige Zukunft. Von Burkhard Röhrig
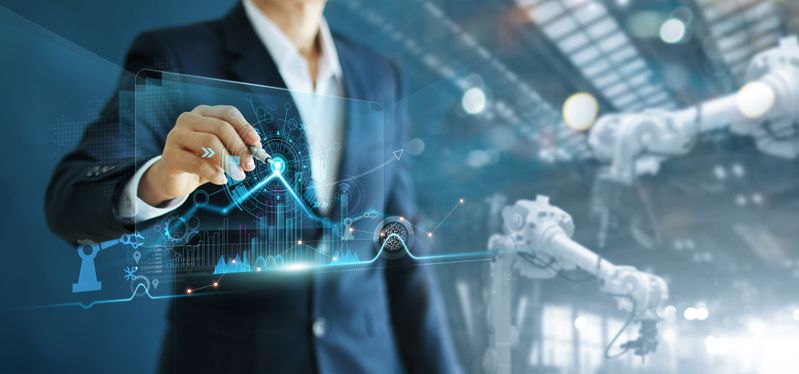
Frei oder nicht frei? Technische Neuerungen haben Prozesse in der Produktion oft nachhaltig beeinflusst und altbekannte und oftmals etablierte Abläufe komplett auf den Kopf gestellt. Derartige Veränderungen und Innovationen sind so tiefgreifend, dass sie von der Wissenschaft sowie der Gesellschaft beobachtet und analysiert, und deren mögliche Auswirkungen in Utopien, aber auch Dystopien behandelt wurden und werden – mal winkt eine rosige Zukunft, in der der Mensch frei und individuell leben kann, mal steuern wir in ein unkontrollierbares System aus Überwachung und Herrschaft der Algorithmen.
Prozesse in der Produktion sind stets im Umbruch
Ob die Erfindung der Dampfmaschine, die Entdeckung der Elektrizität, die industrielle Einführung der Massenproduktion oder die Entwicklung des Computers – das alles sind Meilensteine der Industriegeschichte. Das Zusammenspiel zwischen dem Mensch und seinen Werkzeugen hat sich dabei stets massiv und rasant gewandelt. Was sich dabei ändert ist insbesondere die Rolle und die Verhältnisse der „Akteure“ zueinander – die in sogenannten Akteur-Netzwerk-Theorien behandelt werden.
Wer in die Zukunft der Produktion schauen will, muss daher die Vergangenheit und Gegenwart genau im Blick haben. Denn technologische Neuerungen, die Prozesse effektiver und effizienter gestalten sollen, gab es schon immer. Oft sind es Weiterentwicklungen oder Verknüpfungen von bestehenden Werkzeugen, die letztlich einen Umbruch auslösen.
Während wir bis dato Werkzeuge, Maschinen und Apparate als Hilfsmittel verstanden haben, nehmen sie durch die Digitalisierung und Vernetzung sowie die Künstliche Intelligenz eine eigenständige und selbstlernende Rolle als Akteur ein. Dabei ziehen KI-Systeme Wissen aus großen Datenmengen, erkennen Muster und Regelmäßigkeiten darin und entwickeln – Schritt für Schritt, via Trial-and-Error – eine gewisse Autonomie. Im Kontext der Fertigungsindustrie ist Künstliche Intelligenz damit ein entscheidender Baustein der Smart Factory.
Von Big zu Smart Data
Durch die digitale Transformation, die unaufhaltsam Logistik und Industrie erreicht, fallen schon jetzt viele Daten an. Denn wird jeder Prozess in der Produktion mit moderner Technik überwacht, dann kommen am Leitstand auch entsprechend viele Signale an. IT-Lösungen wie etwa ein Manufacturing Execution System (MES) generieren hieraus nutzbare Informationen. So entsteht ein digitales Abbild der Produktion, das Potentiale und Schwachstellen offengelegt und dem Nutzer hilft, Produktionsprozesse zu verbessern.
Diese Software ist heute auf die Datenerfassung, Auswertung und Visualisierung ausgelegt. Künftig wird sie durch KI erweitert werden, um die Analyse und Steuerung von Fertigungsprozessen selbstregulierend zu automatisieren. Doch dafür müssen die Daten systematisch strukturiert werden – der Schritt von Big Data zu Smart Data ist entscheidend für den Erfolg eines solchen Systems.
Ziel ist es, dass das System Muster und Regelmäßigkeiten erkennt, konkrete Lösungsvorschläge oder Handlungsempfehlungen gibt oder diese gar selbstständig umsetzt und aus den folgenden Ergebnissen lernt und die Prozesse weiter optimiert.
Das Fundament der KI
Das Fundament ist eine saubere und detaillierte Erfassung aller relevanten Daten – hierzu zählen neben Signalen aus Maschinen auch Energiesystemen und Prozessen auch Materialfluss-Daten und dergleichen. Sind solche Informationen bereits vorhanden, ist für die Einführung eines digitalen Produktionsmanagements eine ideale Grundlage geschaffen.
Gleichzeitig erlaubt diese Datenbasis auch das Trainieren von KI-gesteuerten Systemen, da Richtwerte und Kennzahlen aus der laufenden Produktion zur Verfügung stehen. So lassen sich Idealzustände und Störungen definieren, sodass das KI-System auf ein Ziel hin ausgerichtet werden kann – denn sind keine Daten vorhanden oder ist das initiale Trainieren nicht möglich, muss das System über einen längeren Zeitraum selbst testen und analysieren, um effektiv arbeiten zu können.
Die nächste Stufe der digitalen Transformation
Während aktuelle Systeme bereits effektiv arbeiten und ganze Produktionen nachhaltig optimieren, hebt KI das digitale Produktionsmanagement auf eine höhere Stufe: Beispielsweise können eine Personalbedarfsermittlung und die Personaleinsatzplanung mit Smart Data angereichert werden, was dazu führt, dass zukünftige Personalplanungen deutlich mehr Faktoren berücksichtig können, als heute üblich. Welcher Produktionsauftrag benötigt welche Ressource? Zu welcher Zeit, mit Blick auf andere Aufträge, Lieferfristen und Dienstplanwünsche von Angestellten, kann diese Ressource bereitgestellt werden?
Das KI-System vernetzt dazu alle relevanten Bereiche und Daten, lernt die Zusammenhänge und Abhängigkeiten in der Wertschöpfungskette und findet darauf basierend Muster und Regelmäßigkeiten. Die KI reagiert mit jeder Planungs- und Rückmeldeschleife feiner, ihre Prognosen werden genauer und die Planungen damit effektiver.
Prozesse in der Produktion: Auch die Instandhaltung kann digitalisiert werden
Ähnliches gilt in der Instandhaltung. Die KI nutzt die immensen Daten aus der Produktion, um Zusammenhänge zu erkennen, die zu Störungen führen. So lassen sich Wartungsmaßnahmen früher planen und in die Auftragsplanung integrieren.
Beim Einsatz einer KI ist es sinnvoll, eine Art Soll-Zustand zu definieren. Dann „weiß“ das System, worauf es hinarbeiten muss und tut dies selbstständig. Richtig implementiert, führt dies zu einer hohen Kostenersparnis durch die Steigerung von Effektivität und den bestmöglichen Einsatz der vorhandenen Ressourcen.
Hier spielen Maschinen- und Betriebsdaten aus der Produktion eine elementare Rolle, wie sie mit Hilfe von Manufacturing Execution Systems strukturiert erfasst werden. Sie bilden die Grundlage, um das KI-System initial zu trainieren und den Ist-Zustand einer Fertigung zu setzen – vergangenheitsbezogene Daten aus Produktionsprozessen, Transport- und Rüstzeiten, Energiedaten und dergleichen werden vom KI-System also genutzt.
Hinarbeiten auf den Soll-Zustand der Prozesse in der Produktion
Eine KI-basierte Produktionssteuerung arbeitet also effektiv und aktiv an der Erreichung der Unternehmensziele mit. Um solche Projekte umzusetzen, arbeiten MES-Anbieter wie die GFOS mbH mit hochspezialisierten Firmen, die produktionszentrierte KI-Forschung- und -entwicklung betreiben, zusammen. Solche Kooperationen sind der Garant für einen exponentiellen Unternehmenserfolg.
Vielversprechende Pilotprojekte gibt es besonders im Bereich der Feinplanung mit großen Potentialen für weitere Optimierungen. Denn das feinteilige Zusammenspiel von Logistik, betriebsinternem Materialtransport, Bestückung und Umrüsten von Maschinen und Arbeitsplätzen ist entscheidend für eine zeit- und qualitätsoptimierte Produktion. Die Echtzeitüberwachung solch komplexer Prozesse durch professionelle MES-Lösungen sowie die Einbindung von Machine Learning und KI erzeugt eine große Flexibilität im Produktionsalltag.
Abweichungen von der Feinplanung werden automatisch erkannt und Prozesse autonom korrigiert, um Engpässe, Störungen, minderwertige Chargen und dergleichen proaktiv zu verhindern.
Entscheidungsgewalt über das Produktionsmanagement hat jedoch stets der Mensch, aber seine Hilfsmittel werden durch künstliche Intelligenz bedeutend effektiver. Der Einzug von KI-Anwendungen in die Produktionshallen ist ein entscheidender Schritt zur Realisierung wortwörtlicher smarter Factories.
Ist die Zeit von Industrie 4.0 gekommen?
Die Forschung befindet sich noch in einer frühen Phase und wird sich in den kommenden Jahren stark weiterentwickeln. Die Grundlagen dafür bestehen jedoch bereits. Eine digitale Datenerfassung und die Nutzung eines Manufacturing Execution Systems bieten große Potentiale bei der Prozess- und Produktionsoptimierung sowie bei der nachhaltigen Kostenreduktion und Ressourcenschonung. Pilot- und Teilprojekte bieten die Chance, elementares Wissen aufzubauen und die Funktionsweise der KI-Systeme kennenzulernen und zu optimieren. Denn – vereinfacht gesagt – Künstliche Intelligenz ist ein System aus Systemen, ein stark vernetztes Zusammenspiel aller Prozesse in der Produktion und somit ein hochkomplexes Gebilde, das eine autonome, sich situativ selbst steuernde und konfigurierende, datenbank- und wissensbasierte sowie sensorgestützte Steuerung anstrebt.
Die vierte industrielle Revolution ist im vollen Gange und immer mehr Unternehmen setzen auf die Potentiale einer digitalen, smarten und teilweise schon KI-basierten Produktionssteuerung. Künstliche Intelligenz ist hierbei mehr als nur ein digitaler Helfer – eine tiefgreifende Produktions- und Datenanalyse wird durch KI-Systeme überhaupt erst ermöglicht. Das ist ein Erfolgsfaktor.
Burkhard Röhrig ist Geschäftsführer von Gfos.
Lesen Sie auch: Digital gestärkt aus der Krise: So treiben Unternehmen jetzt Digitalisierungsprojekte voran